Batch Picking vs Wave picking

Here at CartonCloud, we’re committed towards helping clients increase their warehousing productivity. Today we’ll look at batch picking vs wave picking, their intrinsic pros and cons, and which is best suited for certain situations.
Each operation is unique. Yet every operation seeks to maximize productivity and minimize idle-time. If you’re looking for some assistance in maximizing your productivity through automation, then get in touch with our team.
Batch picking
Batch picking is the practice of picking a specific batch of product in bulk. The picker is generally only going to one BIN location and generally picking just one SKU. However, from this, he or she may be fulfilling more than one order at the same time.
Pros
The main benefit addresses the main disadvantage in picking. This disadvantage is the lost time where pickers have to travel back with inventory to dispatch stations. Through batch picking, the picker can pick an entire batch of a single product before returning to the dispatch station, ready to instantly dispatch to one or multiple customers.
Cons
Whilst there’s some good upsides to batch picking, there’s also downsides. Primarily, those with inventory of a large physical size will have personnel who struggle to fit more than a few units in a trolley, thereby negating the benefits. Forklifts are often required in batch picking duties.
Wave picking
Wave picking is the traditional method of picking multiple orders one by one with a pick list. Personnel then sort, pack and dispatch orders. There are variations including inventory type, time of day, type of freight carrier, type of customer and even the type of packaging.
Pros
As we mentioned, wave picking can be allocated at different times of the day to separate zones. An example is freight with temperature storage requirements. Commonly, warehouses will have a number of waves in operation prior to dispatch.
Cons
Upon the picking of goods, these need to be allocated at dispatch stations into individual orders. This slows down progress and productivity. Additionally, as wave picking is often done in teams, some personnel may finish their allocated tasks faster with some idle time.
Other picking styles
There are other lesser known forms of picking used in warehouses globally. These include:
- Single order picking which is as the name suggests and found in smaller warehouses
- Pick and pass where orders picked and sent to another area for later fulfillment
- Order consolidation where multiple SKUs are picked for the same order in unison
CartonCloud can assist with these other picking styles, in addition to currently serving many clients who use either batch picking or wave picking, and some do use a combination of both.
Final verdict
Comparing batch picking to wave picking is a common question we get. The right picking method is based on your type of warehouse, speed of inventory movements, space constraints, personnel available, type of inventory and more.
There is no clear-cut answer, though it can depend a lot on the amount of SKUs you stock and the sell-through rate.
We have commonly seen smaller operations to find success with batch picking and larger warehouses to use the wave picking method. Again, however, this isn’t a fixed rule.
Would you like some help in picking the best solution for your operations team? Feel free to get in touch with our team here at CartonCloud.
Subscribe to CartonCloud
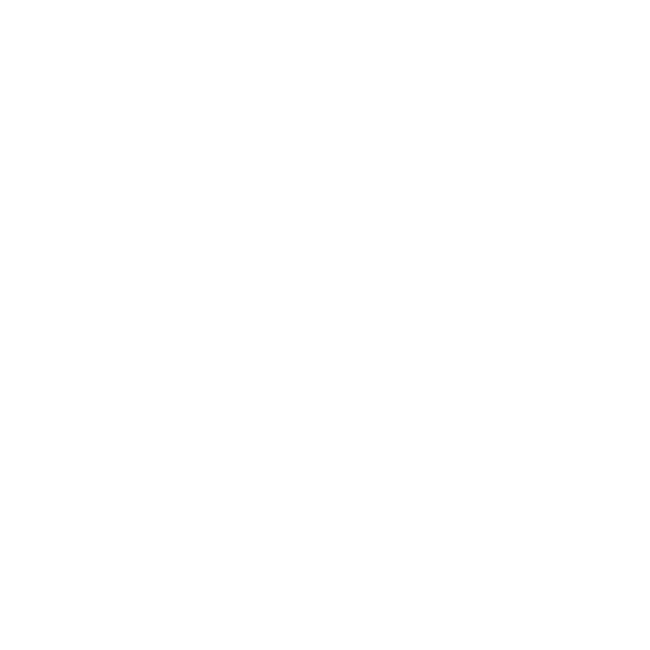