Why your customers will love your cloud-based WMS
Want to win more business with greater customer service? See how you can increase your daily fulfillment and keep your customers happier with the right WMS. Simplify online orders and tracking, automate rates and inventory reporting, and deliver more to your customers with our powerful, end-to-end warehouse management system.
Why your customers will love your CartonCloud WMS
The best cloud-based WMS software for growing 3PLs will have features that allow you to give more to your customers without any hassle or headache on your end. Does it sound too good to be true?
Why use a cloud-based WMS? With a cloud-based warehouse management system, you can deliver greater customer service, easy reporting, and stock transparency, simplified online ordering, and greater accuracy. Your customers will love you for it, and you'll save time and money to grow your business.
With CartonCloud’s top-rated cloud-based warehouse management system, your customers can view their stock levels, stock movement, and order updates 24/7 from their very own user portal login — which means you can keep your customers happy with ease.
What’s more, with our feature-rich cloud-based WMS system, your customers also benefit from your own company’s gains with more efficient operations, minimal errors, streamlined workflow, and seamless invoicing. It’s a true win-win situation.
“Thanks to CartonCloud, we can give the best possible customer service — and our 3PL customers can be as hands-on or hands-off as they want to be” — Deanne Luke, Founder Lexington Logistics.
Give your customers 24/7 Online Portal access
Give your customers eyes on their orders and inventory 24/7 from the customer portal dashboard. They can upload files, view orders and generate their own configurable reports, at the click of a button. They can even set up notifications for low-stock warnings or other triggers, like incoming orders, order fulfillment, and delivery.
Urgent orders? No problems. Your customers can flag priority orders in the system, to be fulfilled urgently under high-priority rates.
A cloud-based WMS like CartonCloud gives you the oversight and accuracy your customers will love.
Want to show your customers all the benefits of your WMS software? We've made a helpful PDF here, that you can share with your customers or win new business. Click the image below to download your PDF
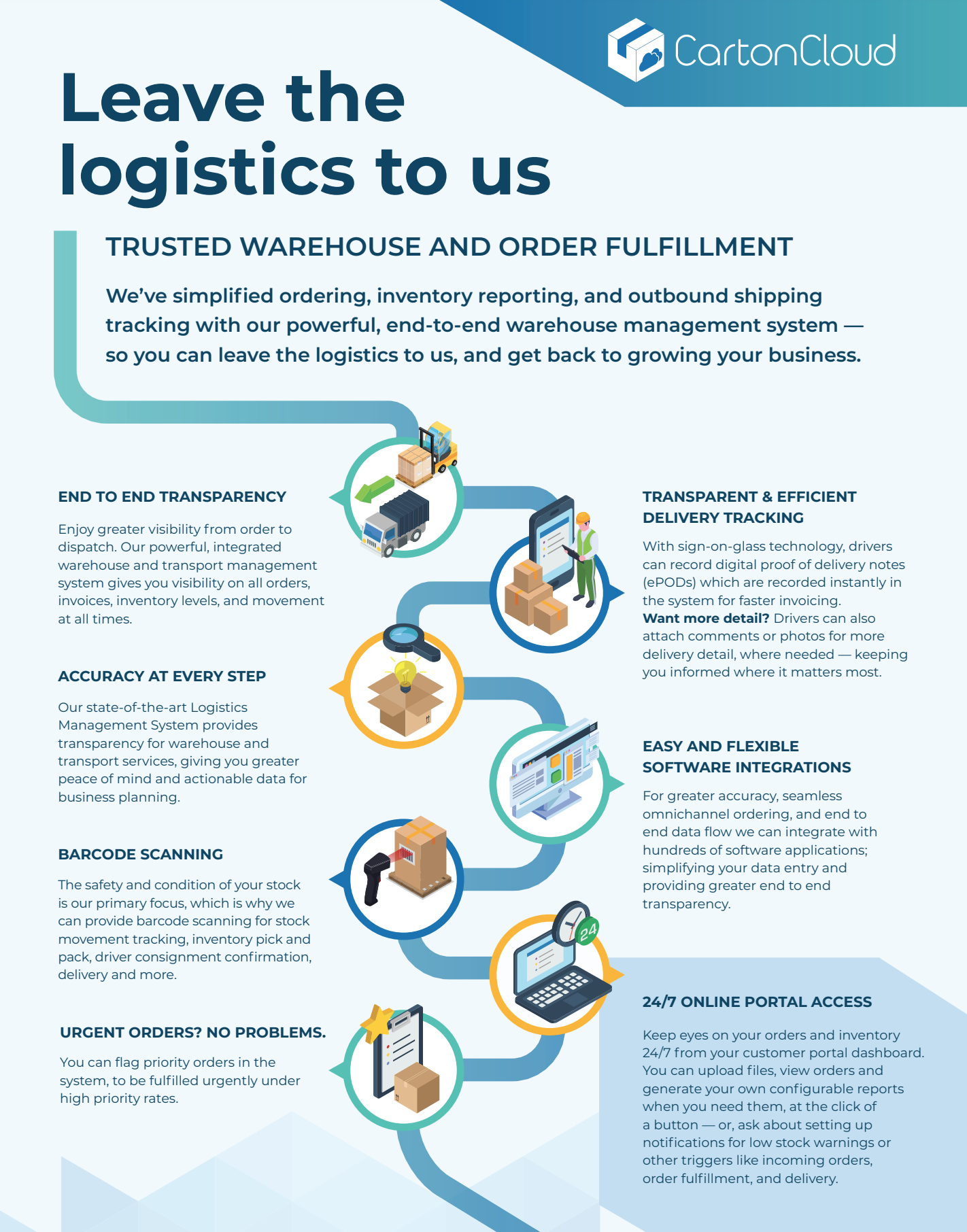
Provide end-to-end transparency
Give your customers greater visibility from order to dispatch, allowing them to track order fulfillment at all times from their own customer dashboard. Our powerful, integrated warehouse and transport management system gives you, and your customers visibility on orders and inventory at all times.
Inventory accuracy at every step
Give your customers greater peace of mind, and go the extra mile with actionable data for your customers to use in their own business planning. With CartonCloud, you can access and deliver your customer's data directly and securely from your WMS, available through their own secure portal log-in.
Imagine telling new customers they will have full access to reporting, inventory levels and order tracking 24/7? Give more to your customers, with ease. With CartonCloud's cloud-base system, your WMS is already gathering data, tracking order status, and delivering up to date reporting, thank to easy workflows like barcode scanning and automated order input.
- Barcode scanning Using barcode scanning for incoming and outgoing orders, you can ensure we have the right product, tracked every time. Ensure the safety and condition of your customer's stock with real-time data captured at each step in the supply chain.
- Smooth, transparent & efficient delivery tracking Drivers can use sign-on-glass technology to record digital proof of delivery notes (ePODs) which are recorded instantly in the system for faster invoicing. Want more detail? Your drivers can also attach comments or photos for more delivery detail, where needed — keeping your customers informed where it matters most.
- Simplified ordering and invoicing with easy and flexible software integrations Eliminate data entry, simplify ordering, and improve accuracy. With CartonCloud, you can integrate with hundreds of software applications, or automatically enter order details from EDI or API, to simplify order input and data sharing, for greater accuracy and full transparency.
Plan for fast-moving stock with replenishment
Optimize your stock locations to have fast-moving or frequently ordered stock close on hand for picking and packing with replenishment. You can access your stock history and check stock movement in your WMS data stored in the cloud, to see what stock is moving the fastest, and then optimize your stock locations in the warehouse for faster access. If you know you have high-frequency orders on a certain item, you can locate it at BIN locations closest to the receiving and dispatch areas.
Not only are you reducing labor time and unnecessary wear and tear on machines, but customers with high-frequency stock also benefit from more efficient order fulfillment.
Simplify navigation with racking barcodes
Plan your warehouse location efficiency to maximize capacity, and with barcode racking labels, you can maximize picking accuracy as well. By setting up warehouse location barcodes, you can simplify warehouse navigation and picking and update them with up-to-date inventory data as you go. It also allows you to simplify storage charges based on warehouse locations for more efficient invoicing and rate transparency for your customers.
Empower your staff with more information and streamlined processes, and keep your inventory levels up to date for customers.
Check out our FREE, helpful Warehouse Hacks Guide for handy tips to streamline your warehouse from end-to-end.
Simple, online stocktake for each customer
Stocktake has never been more simple, thanks to cloud-based inventory management software. With CartonCloud's stocktake module, you can perform complete stock reconciliation for each customer, with greater accuracy and faster reporting.
The stocktake module allows you to split stock onto separate lines for counting based on attributes such as Batch, Expiry Date, or any other custom field set up against the Purchase order Product giving you more control over how you wish to count stock for each customer. Once the stocktake is completed, the system can automatically generate a final report which can be exported as an excel spreadsheet and sent directly to your customers.
Benefit from continuous software enhancements to your cloud-based WMS
With a cloud-based WMS, your warehouse manager's focus can be on continuous improvement. CartonCloud’s logistics software was founded in a 3PL warehouse, designed to streamline day-to-day logistics —and this is still the case. We’re working day in and out to ensure our software remains the top pick for SME logistics businesses, with regular product updates and enhancements based on customer feedback and our ideas portal.
This means you and your customers can enjoy leading logistics software, designed for your needs.
Say yes to partnerships and more! Onboard your network, with CartonCloud Link
CartonCloud’s integrated software is ideal for logistics networks. You can streamline your system between vendors, integrate order and consignment details, streamline invoicing and so much more with CartonCloud Link.
CartonCloud Link connects two separate CartonCloud accounts so data can be passed in both directions as required, sending information such as consignments, PODs, orders, status updates and more.
Want to know more?
Contact our friendly team today for a free demo, or speak to the integrations team about setting up CartonCloud Link with your network partners. We're ready to help you win new business, and give your customers more to love!
Updated June 26 2024
Subscribe to CartonCloud
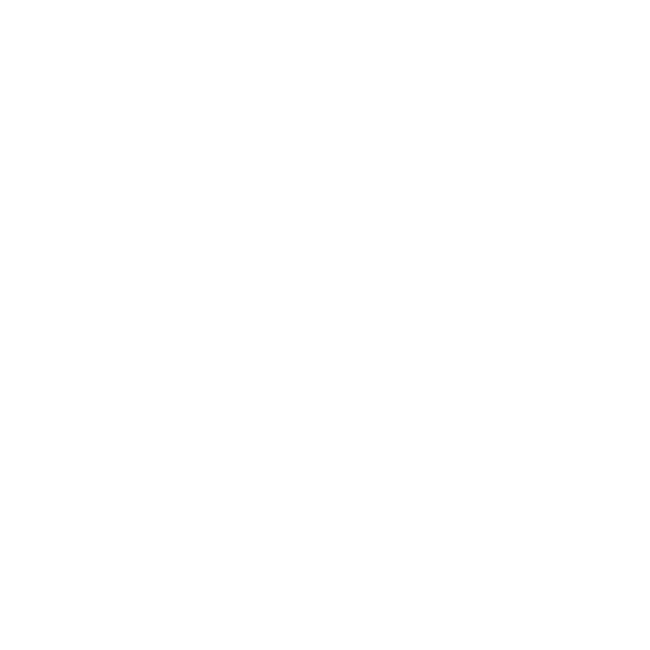