How to achieve a successful warehouse stocktake
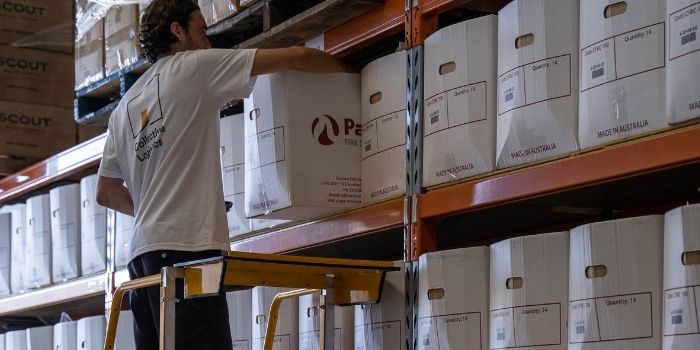
Stocktake... the word that can create an audible groan from any warehousing team — but it doesn't have to be this way! With goods coming and going on high rotation, it is easy to lose track of what is where in your warehouse or forget to update reports in your warehouse management system. However, with the right system and workflows in place, you can ensure a fast, accurate and successful stocktake every time.
Completing a warehouse stocktake is an essential chore for all 3PLs, 1PLs, and even lounge-room businesses. regardless of your company size, your resources, or inventory, it's essential to know what you have, where it is, and any specific inventory details like expiry dates, batch numbers, etc. Having the right 3PL warehouse software can make all the difference.
Use CartonCloud already? Check out all you need to know about our WMS stocktake here.
Stocktake simplified
Do it your way. You can complete your stocktake using CartonCloud's tablet-friendly WMS web app, or on your PC. Alternatively, it can be completed by printing out a stocktake report where counts can manually be recorded on paper, then recorded into the system later at a workstation.
In this short video, Vincent shows how fast and simple stocktake can be with CartonCloud, using our stocktake feature. The CartonCloud stocktake feature allows you to confirm records from your warehouse management system against what is physically on the warehouse floor. CartonCloud, is designed to simplify complex logistics — making your life easier.
Using our stocktake feature, if there is a variance in stock levels between two locations, you have the option to simply update the location to the stock's physical placement, with the click of a button, instantly aligning your system with the warehouse floor. Simple, accurate, and effective. Take a look at how easy stocktake can be!
Check out these tips to make your stocktake season enjoyable and effective!
6 Tips For A Successful Warehouse Stocktake 💪
1. Be specific 🗓️
An efficient stocktake will provide you with a range of information about the goods in your warehouse so you can undertake any necessary movements, or account for variations to ensure accuracy.
Depending on the stock your warehouse holds and manages, you may want to perform stock reconciliation against data points such as production date, batch number, or expiry date. This provides users with more control over how they wish to count their stock during a stocktake and more information at the end of the process.
2. Automate data entry 📲
Traditional manual stocktakes can be time-consuming and prone to error, making the whole exercise redundant. Taking the process into a digital environment and entering stock counts and details directly into a web app is the most efficient and accurate way to complete a stocktake.
By putting all the information into a digital format, you will find it much easier to organise and manipulate the data.
3. Pause stock movements ⛔
This one may seem obvious, but it needs to be said. Before commencing stocktake it is important to let all of your warehouse staff know not to action any sales orders or purchase orders, as this will cause issues with counting quantities and lead to incorrect results.
Again, by taking the process digital you can easily alert all warehouse staff that they are not to move stock in or out for a certain period of time.
4. Split up the work 👌👍
Stocktake can be a big undertaking and you want to get back to normal operations as quickly as possible. To get through the job quickly you can split the counting process to multiple staff electronically by assigning each staff member a section of the warehouse to count — something that can be simplified and done with accuracy when using a digital platform like CartonCloud.
CartonCloud WMS also supports multiple-warehouse records and management, allowing you to manage stocktake activities in multiple locations with accuracy.
5. Capture billable stocktake rates 🙋
Regular stocktakes will provide your clients with valuable information about their goods that will allow them to do their own planning and better manage their supplies. Like all other warehouse services on offer, stocktake rates can be captured easily within CartonCloud using rate cards.
If you wish to charge for stocktake, this can be achieved by simply adding a manual charge to the customer's invoice in CartonCloud. Your stocktake is also a great time to double-check warehouse locations and location charges in your system.
6. Use the data! 🎉
Once you've completed your stocktake, you have a huge amount of data at your disposal, which can be used to build projections and inform business decisions.
Using a platform specifically designed to give users a range of insights once you have completed the stocktake can help improve the efficiency of your warehouse. CartonCloud's Business Intelligence dashboard provides data analysis and tracking, to help you get the most of your data and make informed decisions.
Why choose CartonCloud?
There's a reason we're the favourite warehouse management & transport management software for 3PLs and 1PLs. Our logistics software is made by logistics people, for logsitics people, to simplify your life and allow you to grow your business.
To learn more about our new Stocktake Module using CartonCloud visit our CartonCloud Help Article here.
Page last updated 9 June 2023
Subscribe to CartonCloud
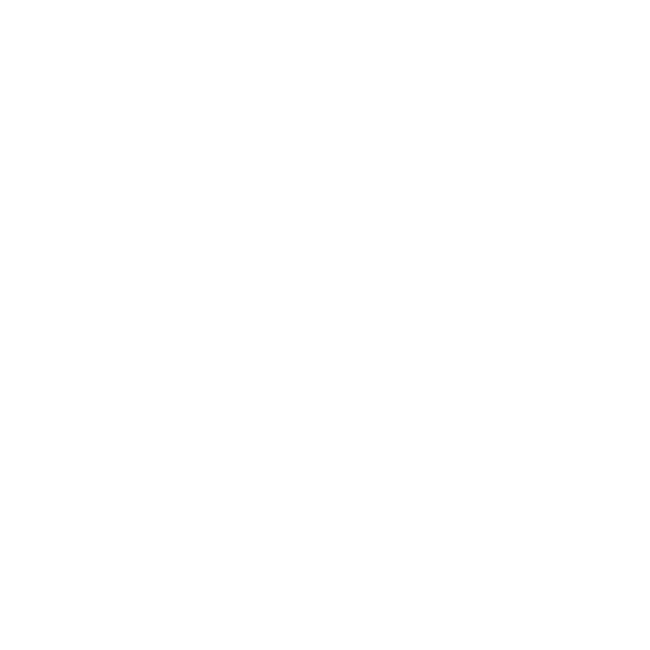