What does FIFO mean?

A common question we hear in warehousing workflow set up is, “What does FIFO mean?” You may have heard the term but aren't sure what it means, or be wondering if this is something you should be considering for your own warehouse. FIFO can help you to optimize your warehouse storage and workflows, to ensure you have the highest operational efficiency, tailored to your stock, and customer needs.
In warehousing, FIFO is used to refer to a system of warehouse storage meaning first-in, first-out.
Using FIFO warehousing means the first items entered into the warehouse are those which are sold first. This way, the stock is rotated through the warehouse, minimizing individual inventory storage time by ensuring the items that have been stored for the longest time are picked first.
The opposite method to FIFO warehouse picking is LILO (Last In, Last Out), whereby the inventory that comes in first is also picked and dispatched first. LILO can be used where inventory is not perishable, or for high turnover stock, where it is easier to pick from recently entered stock.
Using FIFO or LILO warehouse tactics allows you to optimize your warehouse storage, based on your stock, expiry dates or other time-relevant conditions, and your customer ordering requirements.
Want to know more? Let’s get into the importance of FIFO inventory and how operations regardless of size can benefit.
Should I be using FIFO in my warehouse?
Warehouses stocking perishable products will find a greater ROI by selling the oldest items first, to reduce the likelihood of inventory spoiling or aging past its used-by date. Such inventory might include food, medicine, skincare, and consumables.
Most warehousing and logistics operations already have a strong element of FIFO principles, though often inventory is simply assumed to be older. CartonCloud can help to more accurately represent inventory that is to be dispatched first.
Advantages of First-In, First-Out
The main advantage of FIFO warehouse workflows is providing the ability for warehouses stocking perishable goods to clearly and effectively identify the inventory that needs to be dispatched first, in order to ensure stock is dispatched within it's use-by date.
There may also be a financial benefit, in allowing older items to be purchased at a lower price point, and moved on quickly and efficiently.
Most operations do have a system of sorts in place, though the implementation of warehouse management software can aid in enhancing accuracy, both in-field and at workstations.
Some warehouses simply do struggle with limited space to carry out FIFO operations, but having the right system in place, and using a cloud-based warehouse management system like CartonCloud removes time-consuming manual data entry, enabling even the smallest teams to achieve greater daily order output.
Getting Started
To implement a simplified FIFO strategy, it's important to first consider;
- Type of inventory your warehouse stocks, and how regularly it’s dispatched
- The delicate nature of certain inventory such as wine or other perishables
- Resources and manpower available to rotate stock
- Operational space available to carry out rotations
- Location of inventory and economic return of tasks
Locating your FIFO stock
You can track inventory expiry and other important information during warehousing through CartonCloud, either through barcode scanning on entry or by adding the information into custom fields, which will then be displayed when the barcode is scanned for picking.
Inventory can also be physically marked with time and date of receiving, or stored within a specific area of the warehouse to assist with stock identification. When using warehouse location barcodes, this information can again be displayed by simply scanning the barcode for that warehouse location or pick bin.
The bottom line
Some operations do not require any implementation of a FIFO strategy, whilst most do. Rolling out the right solution is necessary to avoid stock losses and to create a greater return on inventory spend.
CartonCloud can help in not only creating a more robust and accurate First-In, First-Out solution but also optimizing a warehouse and its freight operations.
We’re currently helping hundreds of clients, paired with thousands of users, to really enhance their operations.
Book in a time for your free demo to see our software in action, and see if we’re the right fit.
Subscribe to CartonCloud
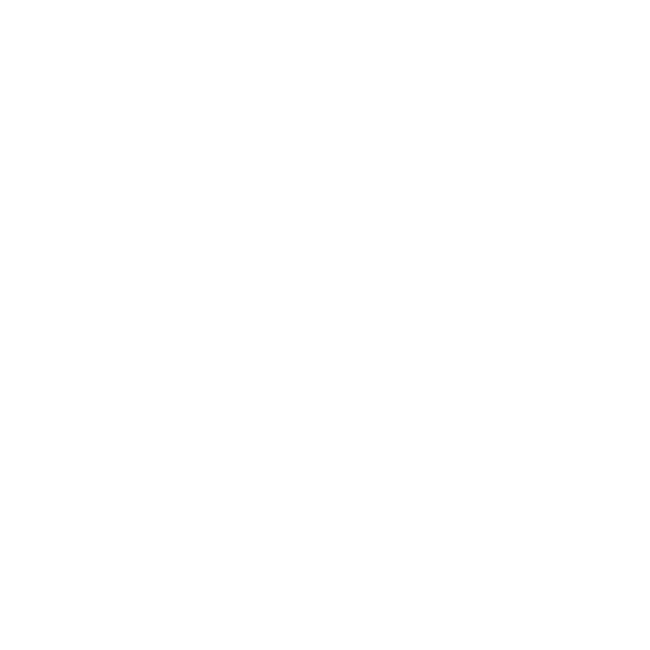